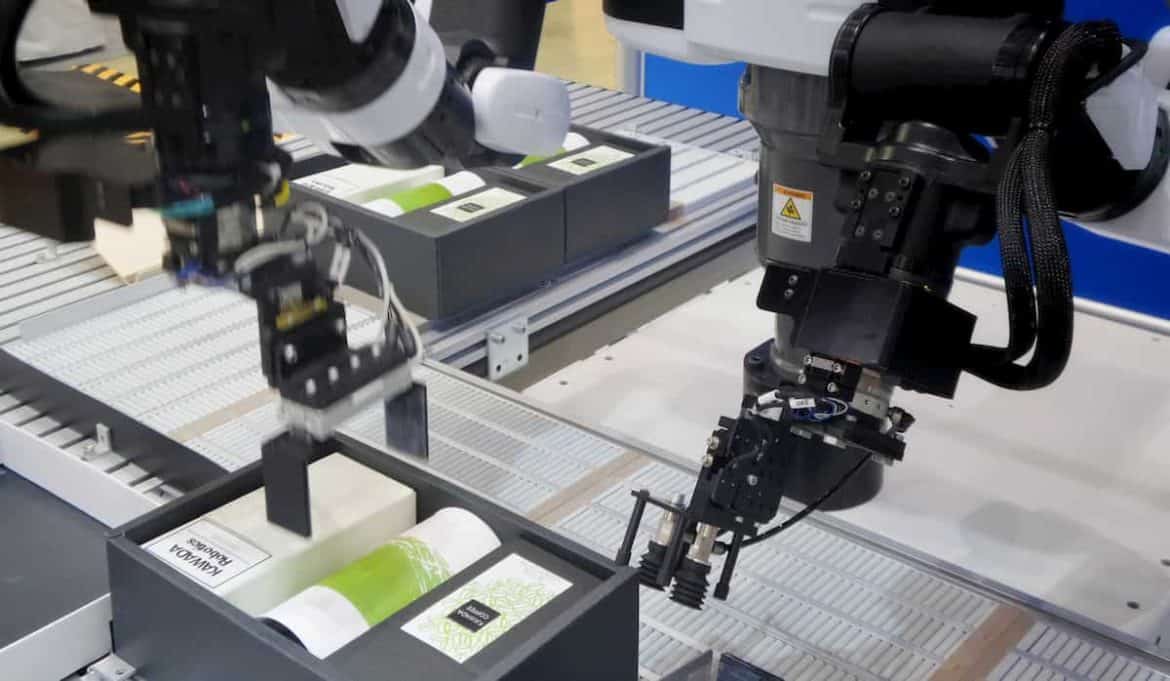
China, Japan and US controls 60% of global installations of industrial robots
The demand for industrial robots has been on the rise in recent years as the manufacturing sector continues to grow in different parts of the world. Despite the installation of industrial robots being characterized by unique challenges, some regions are emerging as frontrunners in leveraging on the technology.
Data presented by Buy Shares indicates that China, Japan, and the United States cumulatively control about 58.71% of the global industrial robot installations. As of September 2020, there were 381,000 units of industrial robots globally. China accounts for the largest share at 140,500 units, followed by Japan at 49,900 units. The U.S is third with 33,300 installed units.
The research also overviewed the annual installation of industrial robots worldwide between 2009 and 2019. Between the ten years, the installation grew by 535%. Notably, in 2018, the installation stood at 422,000 before dropping by 9.7% to 381,000 in 2019. The drop was the first in seven years.
The growth of robots in manufacturing
An industrial robot refers to a system used for manufacturing. Industrial robots are automated, programmable with the capability of movement on about three, or even more axes. Industrial robots are mostly used in welding, painting, assembly, disassembly, pick and place for printed circuit boards, packaging and labeling, palletizing, product inspection, and testing. Most of the robots are tailored towards achieving high endurance, speed, and precision. Most of the industrial robots used in the highlighted countries exist in five major categories including cartesian robots, gantry robots, SCARA robots, articulated arm robots, and human-assist robots.
The rise in industrial robots is mainly fuelled by manufacturers attempting to cut on production costs. Notably, the leading countries with high installation are some of the leading manufacturers in the automotive, electrical, and electronic, and pharmaceutical sectors. In general, the deployment of robots is key in cutting operational costs, reducing errors in the operational workflow, reducing material wastage.
Notably, the cost of raw materials in the highlighted industries is very high hence the need to avoid errors that can lead to wastage. Robots are the better option because they are characterized by multitasking, flexible to handle repetitive tasks with accuracy, and are deployed in critical areas in the course of production lines.
From the data, the Asia Pacific region is also expected to remain dominant. The region’s growth is driven by rising automation, manufacturing industries. Furthermore, the rising population and disposable income is increasing the consumption of consumer goods putting more pressure on manufacturers to adopt robots. Regions like Europe are currently witnessing a peak in manufacturing hence they will become the focus for the industry in the coming years.
Drivers for the industrial robot market
The industrial robot market is also expected to grow following the unprecedented situation as a result of the coronavirus pandemic. In the course of the crisis, many factories had to protect their employees by shutting down some production plants. The pandemic creates a potential market for the industry as it is part of preparing for any similar pandemic in the future.
Additionally, the capability of robots in fighting such a pandemic emerged in March this year. For example, Chinese hospitals ordered about 2,000 UVD robots to help in detecting viruses and bacteria through ultraviolet light and kill them.
Notably, the emergence of the smart factory is playing a key role in boosting the industrial robot market. Manufacturers are concentrating more on research and development activities on how to integrate artificial intelligence into industrial robots. Interestingly, venture capitalist firms are now eying the industry showing intent to fund manufacturers for designing, and testing robots.
Although industrial robots have been taunted as a game-changer, some manufacturers are facing some challenges in implementing the systems. There is a need for having employees with special skill sets to operate the robots which require a new level of expertise. Industrial robots also introduce many new safety hazards and manufacturers have to prepare for this before the robots are installed. Additionally, the cost of the system is holding many countries back from implementing industrial robot units. The system requires typically a large upfront investment although prices are steadily dropping.